What's a Frequency Inverter?
Frequency inverter also called frequency converter, it is a power control conversion device to convert normal power supply (50Hz or 60Hz) to another frequency power by inner power semiconductor on/off behaviors, to control electric motors in variable speed operations. Variable frequency control is changing the frequency supply to the motor stator windings to achieve variable speed control purpose.The frequency inverter is mainly consisted of rectifier (AC to DC), filter, inverter (DC to AC), braking unit, drive unit, detection unit and micro processing unit etc. The control circuit controls main circuit, the rectifier circuit converts AC power into DC power, DC intermediate circuit smoothing the rectifier circuit output, then the inverter circuit reverse DC current into AC current again.
What's new?
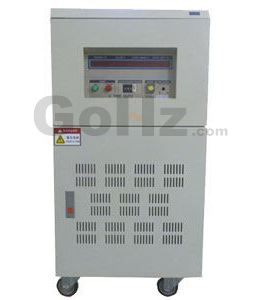
Convert single phase
110V 60Hz to 220V 50Hz;
230V 50Hz to 110V 60Hz;
120V 60Hz to 240V 50Hz;
... ...
Convert three phase
480V 60Hz to 400V 50Hz;
380V 50Hz to 460V 60Hz;
... ...
Both Hertz and Volts are adjustable in separate with better output pure sine wave.
A single phase to three phase converter is a three phase star connected squirrel cage induction motor. It converts 380V single phase 50Hz (across UV input) to 380V three phase (UVW) with a slight unbalance (5%) in Voltage. It is used extensively on railways 25kV 50Hz electric locomotives for driving 150kVA three phase motor load of auxiliary drives like compressors, blowers, pumps...........more than a dozen.
Imagine a three phase motor running from three phase input; then one line gets disconnected. What happens may surprise many; the motor continues to run and deliver the load (but reduced torque) with slight drop in speed.The Voltage across the three phases remains (almost) unchanged and an unbalance of 5% may be expected. If balanced three phase output is required; Static inverter route is fine (as practiced in modern 25kV electric locomotives).
Imagine a three phase motor running from three phase input; then one line gets disconnected. What happens may surprise many; the motor continues to run and deliver the load (but reduced torque) with slight drop in speed.The Voltage across the three phases remains (almost) unchanged and an unbalance of 5% may be expected. If balanced three phase output is required; Static inverter route is fine (as practiced in modern 25kV electric locomotives).
Frequency converters can be powerful tools in maintaining processes by using diagnostics to solve frequency inverter performance issues and troubleshoot related processes. An understanding of how the frequency converter interacts with the process can help you improve overall production and product quality. Many faults are caused by misapplication of the frequency converter. Process changes, such as variations in load or speed; power issues, such as capacity switching by the utility; or changes in environmental operating conditions are not immediately obvious, but could be a major contributor to frequency converter failure. Evaluate the consistency and condition of the process when trying to determine the cause of failure.
I'm hearing about using a frequency converter with my pump and motor
setup for better flow control instead of control valves. Is it worth it?
Do I still need some measure of flow control besides a shut-off valve? I think a frequency converter control can offer better efficiency, but
diminished control accuracy, response time and shut-off performance.
A frequency converters solution is no different than controlling the speed of a steam turbine in order to regulate flow from a compressor. It's just becoming more common, with advances in electronics and with the increased availability of frequency converters and motors for this service.
A frequency converters solution is no different than controlling the speed of a steam turbine in order to regulate flow from a compressor. It's just becoming more common, with advances in electronics and with the increased availability of frequency converters and motors for this service.
Frequency converters are becoming almost standard part of aquatics equipment room packages. Most frequency converters are fairly simple to install and operate however, they are quite complex with respect to their sophisticated hardware and software implementations. Frequency converter functionality and operation can be greatly improved by understanding basic frequency converter theory, terminology and interfacing options.
The prime and immediately tangible target for saving energy using frequency inverters is old mechanical systems, typically using centrifugal pumps and fans, that vary the flow of either water or air in a building or industrial facility. To identify, frequency inverter manufacturers are making it as easy as possible to calculate possible savings, providing PC and even iTunes applications in addition to the know-how for doing the quick hand calculations on-the-spot to quantify potential energy savings.
Putting a contactor on the output of the frequency inverter will assure immediate removal of voltage from the motor which is what you want. On the other hand, some inverters are easily damaged by switching on their output and that it's possible that the motor could be reconnected to the output of an inverter that was operating above zero frequency and this could also damage the inverter. (Effectively a direct (non-soft) or full-voltage start on the output of a frequency inverter)
Flux vector frequency inverters use a method of controlling torque similar to that of DC drive systems, including wide speed control range with quick response. Flux vector frequency inverters have the same power section as all PWM frequency inverters, but use a sophisticated closed loop control from the motor to the frequency inverter's microprocessor. The motor's rotor position and speed is monitored in real time via a resolver or digital encoder to determine and control the motor's actual speed, torque, and power produced.
Applying a frequency inverter to a specific application is no mystery when you understand the requirements of the load. Simply put, the frequency inverter must have ample current capability for the motor so that the motor can produce the required torque for the load. You must remember that machine torque is independent of motor speed and that load horsepower increases linearly with rpm.
Reflected waves caused by a cable-to-motor impedance mismatch are prevalent in all frequency inverter applications. The magnitude of the problem depends on the length of the cable, the rise-time of the PWM (pulse width modulated) carrier wave, the voltage of the frequency inverter, and the magnitude of the impedance difference between the motor and cable.
Among the most successful strategies managers have at their disposal for controlling electrical energy use and minimizing utility costs is the use of frequency inverters. Incorporating frequency inverters into applications such as fans, pumps, and cooling towers can reduce energy use up to 50 percent at partial loads by matching motor speed to the changing load and system requirements.
Frequency inverters are used in any application in which there is mechanical equipment powered by motors; the inverters provide extremely precise electrical motor control, so that motor speeds can be ramped up and down, and maintained, at speeds required; doing so utilizes only the energy required, rather than having a motor run at constant (fixed) speed and utilizing an excess of energy.
These guidelines dispel the confusion about matching Frequency inverters (Variable frequency drive) and motors to fans and pumps that are typically encountered in commercial building applications. While the motivation to increase energy efficiency could be financial (reduced energy costs) or ethical (reduce greenhouse gas emissions associated with power production), it is taken for granted that frequency inverters are an easy way to improve energy efficiency in a motor application. And with these noble intentions in mind, the engineer will specify a frequency inverter for his client. Oftentimes, that isn't the end of the story for the engineer.
This application states energy saving reconstruction on ID fan and FD fan of 4# boiler in a Chinese Oil Industry Company, introduces reconstruction purpose, scheme, implementation and principle. It analyses reconstruction effect, especially the economy effect, illustrates meaning of reconstruction. Variable frequency adjustment is an effective way of source saving management.
Some manufacturers' inverters can provide 100% torque at Zero speed without an encoder. A properly rated and designed motor can be provided to operate at Zero speed, full torque (often called 1000:1 speed range motors). This is a very typical motor requirement for Paper Winders and Rewinders, and Steel Coilers and Uncoilers.
When the frequency inverter is installed, it can decrease the pump speed from N1 to N2 with the pipe network resistance curve (1) being unchanged, so the working intersection A transfers to C. At this time, the consumed axis power can be represented by the area of H3COQ2. Compared with H1BOQ2, it is easy to find out that the inverter has prominent energy-saving capacity.
Gozuk EDS1000 series frequency inverter can meet the demand of extruding machines completely, easily achieve the control target, the same time, has the "zero servo" function, which can make the machine has high torque when running at 0 Hz. The automatic energy-saving function will reduce the output current with the change on the torque. This function can not only save energy, but guarantee the reliability and steady of the system technically, which has become the first choice in the extruding machine.
Gozuk EDS2000 frequency inverter has the advantages of high torque, high-precise speed, and complete function. It can test the dynamic operating parameters automatically and adjust correspondently, to ensure the motor works in the best status. Hence, Gozuk inverter can take place of AC servo system for its high performance-price ratio. It is used widely in NC lathe.
Using Gozuk advanced vector control frequency inverter can supply larger torque when the machine runs at low speed and automatically compensate speed change of high-load running. Excellent dynamic, as well as the excellent over-loaded capacity can meet various needs in many fields.
The injection molding machine usually use triple asynchronous AC motor which cann't vary its speed, the constant vane pump which drags and the flux of output hydraulic oil cann't be varied. The plastic machine which operation at the low speed, excess fluid is returned via overflow valves to the fluid supply ,and the energy is wasted.The frequency inverter can adjust the speed of motor according to the function of control system, and can vary the flux of hydraulic oil output from vane pump according to the speed of plastic machine action, and reduce the energy waste of hydraulic oil from overflow valve to oil supply, so to save more power. According to the products of injection, the energy can be saved 20~70%.
1. How much process flow and pressure requirement through AC motors
2. Existing control methodology like control valve in pumps, Damper or guide vane for Fans & Blowers etc. and position of the valve or dampers
3. If you have process flow and pressure data and pump or fan design data, you can calculate energy saving using affinity law
4. Loading and Unloading cycle for compressor application. If the unloading time is higher for compressor application, you will get better energy saving
5. Using affinity law, you can calculate the energy saving with consideration of frequency inverter losses. With this you can calculate the Pay back of the inverters.
There are different ways you can use frequency inverter or soft starter to reduce your energy bill. Carefully analyses the possibilities of your plant.
2. Existing control methodology like control valve in pumps, Damper or guide vane for Fans & Blowers etc. and position of the valve or dampers
3. If you have process flow and pressure data and pump or fan design data, you can calculate energy saving using affinity law
4. Loading and Unloading cycle for compressor application. If the unloading time is higher for compressor application, you will get better energy saving
5. Using affinity law, you can calculate the energy saving with consideration of frequency inverter losses. With this you can calculate the Pay back of the inverters.
There are different ways you can use frequency inverter or soft starter to reduce your energy bill. Carefully analyses the possibilities of your plant.
Generally frequency inverter has following control modes: open loop vector control, V/F control, open loop torque control, closed loop vector control, slip frequency control.
Open-loop vector control inverter
Apply to high performance general-purpose application with no PG encoder, one frequency inverter controls an electric motor only. Such as machine tools, centrifuge machines, wire drawing machine, injection molding machine, etc.
Open-loop vector control inverter
Apply to high performance general-purpose application with no PG encoder, one frequency inverter controls an electric motor only. Such as machine tools, centrifuge machines, wire drawing machine, injection molding machine, etc.
The frequency inverter designed for lifting industry application has a good torque control performance with advanced control technologies. Its reliable braking control, quick stop, DC excitation control, master-slave control technology to ensure the safety, reliability and high efficiency in lifting industry application. For different requirements in lifting industry, there are translational structural frequency inverter, full inverter, dynamic braking frequency inverter and a variety of mature application for users. Frequency inverters are widely used in lifting machinery for lifting, pitching, luffing, wheelbarrow, gyration, grabing.
What is more important in a frequency inverter? Ac line reactor or a DC choke? If Ac line reactor is missing what are its possible impacts? What if DC choke is missing?
AC line reactors reduce current harmonics on AC line which is caused by rectifier, while DC choke deal with DC bus current.
AC line reactors reduce current harmonics on AC line which is caused by rectifier, while DC choke deal with DC bus current.
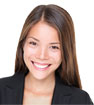
Search inverters
Category
inverters
Featured
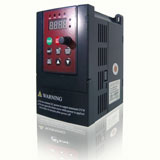
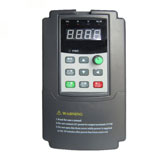
Recent
60Hz to 50Hz Frequency Converter
50Hz motor running on 60Hz power supply
Single phase to three phase converter
Frequency converter typical shortcomings
Frequency Converter Troubleshooting
Frequency inverter, the best energy saving solution
Does Frequency converter better than control valves in flow controls
Frequency Converter for Pumps
Why AC motor needs a Frequency Converter?
Determining frequency converter size
Frequency inverter energy efficiency calculation
Frequency inverter for heavy duty application (mining)
50Hz motor running on 60Hz power supply
Single phase to three phase converter
Frequency converter typical shortcomings
Frequency Converter Troubleshooting
Frequency inverter, the best energy saving solution
Does Frequency converter better than control valves in flow controls
Frequency Converter for Pumps
Why AC motor needs a Frequency Converter?
Determining frequency converter size
Frequency inverter energy efficiency calculation
Frequency inverter for heavy duty application (mining)